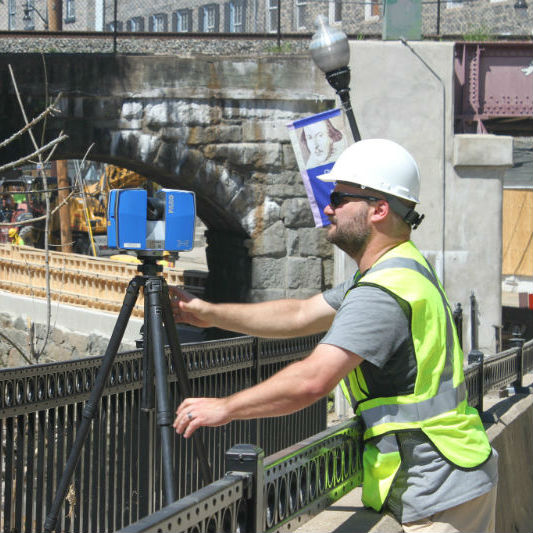
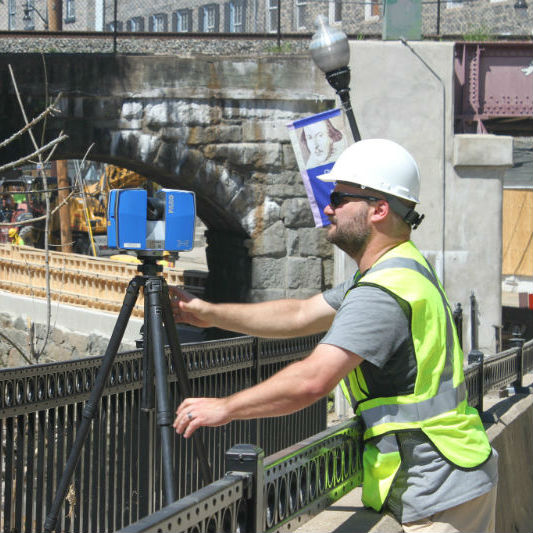
February 21, 2017
Preservation through Lasers with Joe Nicoli of Direct Dimensions
Podcast me up, Joe! This week’s episode is all about lasers. Our guest, Joe Nicoli, works with Direct Dimensions to create valuable 3-dimensional scans of historic sites and a wide variety of items. Listen and learn more about how lasers are used in the everyday work of historic preservation, and how laser scanning may be about to revolutionize how we document sites and artifacts.
Introduction
[Nick Redding] Hi, this is Nick Redding and you’re listening to PreserveCast. Lasers, no longer the technology of the future. Today’s guest, Joe Nicoli, demonstrates that laser scanning is very much of the present day. Get ready to learn about how Joe uses laser scanning to help preserve everything from whole buildings to the fingerprint off a piece of a thousand-year-old pottery as we get beamed up into PreserveCast.
From Preservation Maryland Studios in the historic podcast district of Baltimore, this is Preserve Cast.
[Nick Redding] This is Nick Redding and you’re listening to PreserveCast. Joe Nicoli is an archeologist and the heritage scanning specialist for Direct Dimensions, a company based right here in Baltimore, Maryland that offers assistance with a wide variety of 3D technologies. He has over 15 years of experience with laser scanning and before joining Direct Dimensions in 2012, he mapped and laser scanned hundreds of historic and archeological sites for the National Park Service and other clients. Thanks for being with us today, Joe. Welcome to the PreserveCast studios.
[Joe Nicoli] Thanks for having me.
[NR] So we have so many questions for you and I think that the work that you do is something that just gets people excited. They find it really fascinating. And I think it brings a lot of interest to the work that all of preservation is doing. So how did you get into this? What was your path to laser scanning? How does someone become a laser scanner?
[JN] Well, my background’s archaeology. So I started out in archaeology – did a little bit of digging – ended up working for the National Park Service for a short time doing preservation work, just stuffing mud and mortar. This was in northern Arizona, that was just a summer gig. And while I was doing that, my supervisor on that job was going to work for a company that did traditional survey mapping for archaeology firms. So when a road or major building, federal or state funded project is going in, all the archaeology has to be cleared out of the way before that road can go in. Especially out west, where there’s stuff in the ground everywhere. There’s firms that specialize in that. They’re on the East Coast, too, but there’s a lot of them in Arizona. And so I worked for a company that we did traditional survey mapping, so we did total station and GPS mapping to locate all of the archaeological finds that were in the right-of-way of a project coming in. And so I did that for a couple of years, and from there, we got into laser scanning. That was where the laser scanning started – it was in about 2001. And there’s some earlier versions of it, of different scale, but for us it came out of survey into laser scanning around 2001. From there we started doing more standing architecture work, so we did a lot of the big structures for the National Park Service.
[NR] So why don’t we talk a little bit about laser scanning because I know we kind of jumped right into it, and obviously that’s a lot of what you do, if not almost all of what you do. I think a lot of people think of lasers, and maybe the most experience they’ve had with them is either a laser pointer or they’ve gotten Lasik done on their eyes, but it’s totally different what you’re doing. So why don’t you take us through sort of, you get to a site and you do what? You open up your case and what do you have there and how do you use it?
[JN] Okay, so the laser scanner is, these days, it’s the size of a toaster, and it sits on top of a tripod. So you set up your tripod, you set the laser scanner on top of it, and then it works essentially the way a range finder does – like if you’ve got a golf range finder. If you’ve got one of those little distometers that you’re doing work on your house or something. It works on the same principles; so a pulse of light goes out from the laser scanner, goes out, hits a surface, comes back. The time it takes to do that, speed of light calculation, you get a distance. The ones that are out there now, they do that 500,000 times a second, and they do it on a really well-known azimuths coming from the center of the laser scanner. So what you end up with is millions and millions of individual points that are collected into this laser scanner.
[NR] And so you can scan, obviously, a physical structure or you could scan an archaeological dig and it’s basically taking all these points and then in a computer, it’s reconstituting them as sort of a 3D visualization of what happened out there. Is that fair?
[JC] Yeah, that’s a fair assessment. In its raw form, it’s millions and millions of individual points.
[NR] So it’s a giant point cloud.
[JC] Exactly what it’s called. It’s called a point cloud. It’s non-penetrating so it only sees what it sees. So to do a whole site, you have to set up this scanner at a number of locations around it.
[NR] It can only shoot what it sees basically. So if you’re doing a building, it can only get you the front side until you take it around back.
[JC] Until you go around the corner or if you go inside, you set up in the door so you can look inside, you can look outside.
[NR] And you’ve done a lot of historic structures I would imagine?
[JC] Yes.
[NR] So is there one that listeners would know? Sort of a nationally significant one that we might be familiar with.
[JN] Oh, man. Since I’ve come to Baltimore, we’ve done the National Cathedral. That was a big one down in DC. We’ve done a lot of work at Mount Vernon.
[NR] Okay, Mount Vernon. How long would it take to do an initial scan of a place like Mount Vernon?
[JN] Well, we had to break that one up just because Mount Vernon never closes so we had to work around their schedule. But a place the size of Mount Vernon, two guys could do that in a day with the current technology – just the main building, not all of the outbuildings and everything else.
[NR] Right, and Preservation Maryland worked with Direct Dimensions after the flood in Ellicott City. Back in July of 2016, Ellicott City faced sort of a devastating flood in the center part of our state here in Maryland where they received over six inches of rain in about two hours. Devastating. And you guys came in and were able to scan that entire historic district, sort of the streetscape of Ellicott City, and capture the impact of that damage and you did that in a few hours.
[JN] A few hours, yeah.
[NR] I mean, it really does move pretty quick. So obviously, you can do physical structures, and then I take it – and I understand because I’ve heard you speak before that there are ways in which you can also scan objects and pieces and things pulled from archaeological sites and museums. Direct Dimensions does a lot of that work, as well?
[JN] Absolutely. Yep. Yes, we do. So we have a number of different technologies. So the technology I described there is called LiDAR scanning, terrestrial laser scanning, terrestrial LiDAR – it has a number of different names. There are different technologies we use inside on small objects. So we like to think of it as in-facing versus out-facing. So when you’re scanning a whole building, you have a laser scanner that’s set up on this tripod, and it’s scanning out from the center point of that laser scanner. When you bring objects into the lab, you’re scanning in. So you’re moving that scanner around the object, capturing what’s inside that space.
[NR] So what kind of objects have you done? I mean, give the listeners sort of a cool example of one.
[JN] We do absolutely everything. We do a lot of artwork, we do a lot of mechanical work. We do implant work, prosthetic work. So you scan this hand – if you lose that hand, you can scan it.
[NR] Wow. And in the heritage field, I mean, what kind of things have you gotten into?
[JN] In the heritage field, we scanned the plaster works for some historic properties down in Annapolis to help inform the new plaster works that went into the renovation of the Old Senate Chamber.
[NR] Okay, and this was at Annapolis. You guys went into historic buildings where they believed that the plaster work in those buildings would have been similar to non-existent plaster work where it would have existed in the Old State House, in the Old Senate Chamber, and so you scanned that. That then was given to the plaster workers to use as they did a traditional plaster work.
[JN] Yeah.
[NR] I mean, that’s pretty neat. Has that been replicated elsewhere? Do you get called on to do that kind of work often?
[JN] We get called in to do it a fair bit. You and I were talking earlier about that medallion.
[NR] Right.
[JN] That’s another typical kind of…
[NR] So Joe is mentioning a medallion where you actually went into a structure near Frederick, Maryland, and you scanned the medallion on a ceiling, and then that medallion was 3D-printed. And that’s the other component of this that we haven’t really mentioned, is that oftentimes a lot of your work can be – if you’d like, you can replicate that, particularly when you’re scanning objects. Does that happen a lot? Do you guys see that happening a lot?
[JN] It does happen a lot.
[NR] And I mean, what’s the purpose for that? What are a lot of people doing with that? Is that for them to have just a copy of it, or what are the applications?
[JN] We’re doing stuff that is full replacement. We had a big project – it was Bergdorf Goodman up in New York where they have that iconic front entrance, and they want to replicate that on the back side of the building. And so what we did was we went in, we scanned the whole front side of the building, both in this kind of larger sense with our more traditional long-range scanners just to get the layout of the building, and then we scanned some of the intricate stonework with some of our higher resolution scanners, and then took all of that data and manipulated it.
The door on the back was a different size than the door on the front, but they wanted them to look the same, so. Once you get it into the computer it’s really easy to scale that data. And so we created patterns for them to make the back entrance have that same beautiful stonework look as the front entrance. And then that data went directly to the stone miller. So a lot of people get really hung up on the idea of printing, but there’s a lot of digital technologies that you can use to mill. So like a five-axis mill machine, you can actually cut things out of stone. It doesn’t have to be 3D printed from this data.
[NR] Wow, so it seems like the applications for this are growing and are immense. And we’re gonna talk a little more about that when we come back to PreserveCast in just a few moments.
And now it’s time for a Preservation Explanation
[Stephen Israel] Hello, it’s producer Steve here, with a preservation explanation. Lasers are no doubt very interesting, but if you are a historical fashionista, something that might have popped out at you from Nick and Joe’s conversation is that fact that Joe worked at the Bergdorf Goodman building in New York City. Bergdorf Goodman is a high end department store that was started by a French immigrant, Herman Bergdorf, in 1899, and his one-time apprentice, Edwin Goodman, as a woman’s tailor. This may seem a little contrary to the rugged Southwestern desert cowboy preservationist image of Joe Nicoli, but stay with us.
In 1928, Goodman, having bought out Bergdorf and grown the business by pioneering the concept of ready-to-wear clothes, took possibly the biggest leap he could with his business; buying a plot of the recently torn down Vanderbilt Mansion property at 5th Avenue and 57th Street, to build an equally iconic home for his legacy. Although built on only a portion of the massive Vanderbilt property, which remains the largest private residence ever built in New York City, the Bergdorf Goodman building is impressive in its own right. The nine floor building features an unusual construction for the time. It had elevators all the way to the top floor, which served as the Goodman family’s private seventeen-room apartment. It was designed by architect Ely Jacques Kahn, and the exterior’s made entirely of white marble. The facade that Joe mentioned maintains a distinct appearance, because the building was originally home to in separate store fronts with Bergdorf Goodmans as the flagship store. Today, literally in the fall of 2016, the building has been granted status as a landmark. Also today, PreserveCast became the place where fancy pants fashion and historic preservation meet. All right, let’s get back and see what Joe and Nick are up to on PreserveCast.
[NR] Hi, this is Nick Redding and you’re listening to PreserveCast. We’re talking with Joe Nicoli, an archaeologist and heritage scanning specialist for Direct Dimensions. So Joe, before the break we were talking about some of the applications for this and how it’s not just 3D printing but it’s also carving and all these different ways in which you can take the data that you guys are producing and go on and do something physically with it in the real world so to speak. But I guess I’m curious, have you seen this kind of technology change even since you’ve been working with it? Has it improved in a way?
[JC] Absolutely. I’ve been doing this 15 years, I already have my back in my day stories about scanners that weighed 50 pounds and 50 pounds of batteries and cords. Couldn’t get them wet and wouldn’t work past 75 degrees and all that…
[NR] So a lot of it is sort of efficiency and the logistics have gotten a lot easier. Are there still limitations? Are there some things you can’t scan?
[JC] It’s getting better, the technology, because it’s light-based obviously, it has limitations. It doesn’t particularly like shiny objects because that will reflect –
[NR] So it kind of bounces off the thing?
[JC] – the light or absorb the light. It doesn’t like black-shiny especially. There’s things like that. There’s ways around it, not generally in preservation work, but you can put a thin coating on the object. That kind of mattes out the shininess and that allows us to scan it. We don’t get into that too much with the preservation.
[NR] Right. You can’t really do it under water at all, right?
[JC] They’re working on some things, but it’s similar problems. So it’s light under water, so the light’s refracting.
[NR] So, it’s bouncing all over the place.
[JC] I mean, it’s in the water, so it gets warped. I know the Navy has been doing some work on it. Probably, for underwater stuff, you’re more looking at 3D photogrammetry – is probably a better option for underwater work. But that’s probably a whole other conversation [laughter].
[NR] Just so that the listener knows, what is photogrammetry?
[JC] Photogrammetry is taking a number of images, from a number of different angles, of an object or it’s big now with all of the drones that are flying around the areas, the idea of aerial photogrammetry. And so you fly a pattern, shooting your camera down. And there’s a lot of overlap between those images. And there are softwares out there now that can convert that 2D image into 3D data. I don’t know the math that allows them to do that.
[NR] And so they’re actually then creating almost 3D models out of photographs. But this is a very different process than what you’re talking about.
[JC] Yes.
[NR] And not quite as accurate as well, because there’s some fudging that’s done in order to get there, whereas yours is extremely accurate. And how accurate can it be? I mean, if you’re doing a scan of, let’s say, Mount Vernon, how close is your point cloud to the real thing?
[JC] It’s probably a quarter of an inch or less. The scanners are rated at three or four millimeters of air.
[NR] So, it’s good enough for construction documents?
[JC] Absolutely, that’s what’s really driving that technology right now. So, while we were at Mount Vernon, we also brought some of our high-resolution scanners. There are other scanners. We brought one down and scanned their plaster works, on the ceilings down there in, I believe, three of the rooms. It’s a sub-millimeter scanner, so, I mean, it’s picking up everything. And then, once you get into the lab, I did a project with an archaeologist associated with Hopkins, and we were actually able to lift a fingerprint off of clay work.
[NR] And that’s a historic fingerprint, though, right?
[JC] It’s, well, archaeological. It was a pot sherd from a dig in Aqaba, Jordan.
[NR] So roughly how old a fingerprint are we talking about?
[JC] Oh, man.
[NR] I mean, thousands?
[JC] Oh, yeah, thousands of years.
[NR] Wow. So, I mean, there’s something to be said for being the first person. And archaeologists talk about this, and I’m sure you’ve had that experience, where you’re the first person to touch something, perhaps since it was dropped a millennia ago.
[JC] Oh, yeah.
[NR] But now you’re the first person to see that fingerprint. Is there a database being created of historic [laughter] fingerprints kind of like track people through history.
[JC] That’s where I give this talk all the time where I talk about that. So, if you’re able to pull off this thumbprint – so Aqaba was kind of a trade center. So if you’re able to pull this thumbprint off a number of vessels and they all have different cultural iconography on the outside of them but they all have the same thumbprint, well then you can say that this one trades person was working for all of these different cultures. There you’re really starting to tell – you’re learning something about the cultures. You’re learning about archaeology. You’re learning about the history and that’s kind of why I liked archaeology in the first place is that trying to fill in the gaps of what we don’t know about how these ancient people lived.
[NR] Yeah, and it seems like that’s a way to fill in the gaps that wasn’t even fathomable 20 years ago, maybe even 15 years ago and now we’re getting so close to that. So where do you see this kind of technology going? I mean you’ve been doing it now, I guess, 15 years professionally and you’ll probably be in it for at least another 15 if not more hopefully. It seems like if you’re getting to the sub-millimeter level, that’s pretty good. How much better can it get? Are there ways in which – I mean are you hearing about sort of the next wave of this or where we could be in 10 years or so?
[JC] There’s a couple of different directions it can go. Obviously what we talked about just from where we were to where we are now. Speed and efficiency, that’s only going to get better. One of the companies just released one that’s about the size of a can of Foster’s and that’s the laser scanner that 15 years ago was the size of –
[NR] Fifty pounds.
[JC] Fifty pounds, yeah.
[NR] So now you’re talking about something that maybe is 5 or 10 pounds max?
[JC] Yeah, so I think that’s where you’re going to continue to go – kind of the same trajectory that GPS went on. And it will become more democratized, too.
[NR] And cheaper, I guess too. Can an individual go out and buy a laser? I mean, you can buy a laser scanner, but I mean what does a unit cost that you’re talking about? The toaster-sized one that goes on a tripod.
[JC] Twenty to thirty-thousand dollars.
[NR] So it’s not something that the amateur is going out to pick up like a drone is. But obviously, it’s moving in that direction, it sounds like. So as you say, there’s – could be sort of a democratization of this.
[JC] Yeah, so there’s definitely that, and I mean, you do three or four jobs. Then it starts paying for itself. Mostly with that unit, that’s going to be servicing the architectural and engineering and construction market and archaeology. So we co-opt everything we have anyway, so.
[NR] So if someone is looking to perhaps utilize this kind of service if they run a historic site or they work for a preservation group and they want to know more about 3D scanning and technology, where would you direct them? I mean, obviously, they could go to Direct Dimensions and could hire you to do that kind of work, which would be good for Direct Dimensions. But if they don’t live nearby or they just kind of want to learn more about it, are there any resources out there that people could look into?
[JC] Oh, sure. There’s some really good ones out there. The Smithsonian launched one not long ago. They have a really good website, a virtual museum of laser scanning things [Smithsonian X 3D Beta], but they don’t get so much into the site-level stuff. They’re more about the artifacts, obviously, because they’re a museum.
[NR] Yeah, I’ve actually held a copy of Abraham Lincoln’s top hat, which they pre-printed out and then brought out to an event. It’s pretty cool.
[JC] CyArk is another one. They’re really a pretty robust reviewer online, so if you want to wrap your head around what a point cloud looks like, you can definitely look at point clouds on their website, and they’re kind of committed on a world stage, and they’re committed to scanning World Heritage sites, so they have some pretty unique ones outside of The US. And then HABS/HAER [Historic American Building Survey/Historic American Engineering Record] is also –
[NR] A division of the National Park Service, the Historical American Building Survey.
[JC] They’re into the laser-scanning space, as well. They have some stuff online. Just as a site, they are working on the ability to have these data sets, these point clouds be preserved as part of the legacy the same way that drawings are.
[NR] And that’s not currently the case.
[JC] They’re not quite there yet. They’re working on digital photography, then they’re going to get to laser-scanning data, but they have some good stuff online. You can look at some of the things that they’ve scanned and some of the stuff that they’ve taken other people’s data and done work with.
The Next Level of Architectural Documentation
[NR] And it seems to be that this really is what we’re talking about or kind of dancing around is that this is the next step for architectural documentation. It goes a level beyond large format photography and sketches, which are great and important, but this takes it to sort of the next step, and that’s an important thing, I think, for preservationists to embrace if someone is hoping to use this on their property or a sight that they manage, what are the costs associated with this? Ballpark, what does it take to get an organization out to scan a building for a day?
[JC] Ballpark, it’s a couple grand to get the data collected.
[NR] Okay, so we’re not talking about – right to get the data collected and then you have to manipulate it and there’s more cost associated with this, but I think the point I was trying to get at is it’s not a $150,000 to get something like this done.
[JC] No.
[NR] This is within the reach of most – even nonprofit organizations that are managing places that really want to document their story.
[JC] Absolutely.
[NR] And then you can also take that story to the Web because now you have a digital representation of this. So it is, in a sense, it’s – you mentioned that it’s becoming more democratized, but in a way it already is. And it definitely is within reach for a lot of organizations.
[JC] Yeah, absolutely.
[NR] So as we sort of draw to the conclusion here, we ask everyone who comes into the PreserveCast studio, a very difficult question for anyone who cares about history or anyone who’s from Maryland which is, what is your favorite building in Maryland? It’s hard to pick them, but do you have a favorite building?
[NR] Favorite building in Maryland… I’ve only been here about five years, so let’s see.
[NR] You’ve worked on a lot though I would imagine.
[JC] I have.
[NR] If you have to go beyond Maryland’s boundaries that’s okay too. This is a national podcast, but it’s based in Maryland.
[JC] [laughter] I will say because I – just because it’s my favorite building ever. There’s a site in northern Arizona called Keet-Seel it is an archaeological site. It dates to the late 1200s and it’s managed by the Park Service. It’s on Navajo land. So it’s a nine-mile hike to get out there but it looks like it was abandoned yesterday. There’s corn cobs on the ground, there’s squash stems on the ground. I mean it looked like people walked away yesterday. It’s just an amazing cliff setting. It’s beautiful.
[NR] Okay, we’ll take it. We haven’t gotten a –
[JC] It’s hard to get there but it’s absolutely worth it.
[NR] We haven’t received a 12,000 year old nomination yet as their favorite site.
[JC] No, it’s 1,200.
[NR] One thousand and two hundred, I’m sorry. One thousand and two hundred. Old enough, though. It might be the oldest one we’ve heard about so far. All right, well it’s been a pleasure talking with you. If people want to get in touch with direct dimensions, how can they do that?
[JC] We’re on the web. Look on our website. My name is on there. You can e-mail me directly.
[NR] And that website is?
[JC] www.dirdim.com – DirectDimensions.com
[NR] Thank you so much. Joe, it’s been a pleasure to have you here at PreserveCast.
[JC] Thank you.
Credits
You don’t need to open a history book to find us and available online from iTunes and their Google Play Store as well as our website: PresMD.org. This is PreserveCast.
This podcast was developed under a grant from the National Center for Preservation Technology and Training, a unit of the National Park Service. Its contents are the sole responsibility of Preservation Maryland and the Maryland Milestones Heritage Area and do not necessarily represent the official position or policies of the National Park Service or the National Center for Preservation Technology and Training.
This week’s episode was produced and engineered by Ben and Stephen Israel. Our executive producer is Aaron Marcavitch. Our theme music is performed by the band Pretty Gritty. You can learn more about them at their website: PrettyGrittyMusic.com, on Facebook, or on Twitter @PG_PrettyGritty.
To learn about Preservation Maryland or this week’s guests, visit: PreservationMaryland.org. While there, you can check out our blog and learn about what’s current in historic preservation. We’re also on Facebook, Instagram, Flickr, and Twitter @PreservationMD. And of course, a very special thank you to our listeners. Keep preserving!
Previous episode